Selecting the Right PVC Granulator for Your Needs: A Guide to Key Considerations
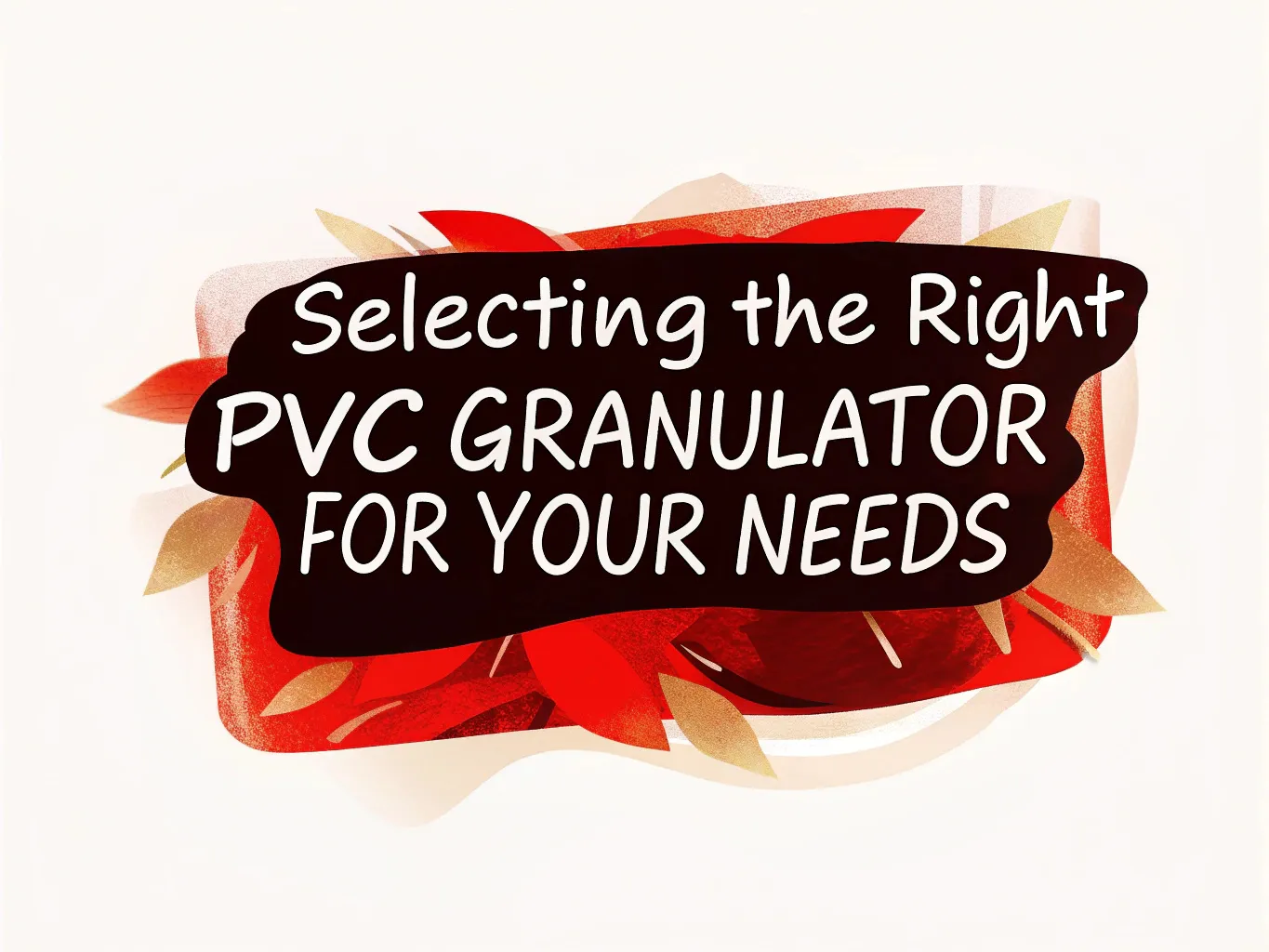
In the realm of PVC (Polyvinyl Chloride) recycling and processing, choosing an efficient and reliable PVC Granulator is a critical step towards ensuring smooth production workflows, reducing operational costs, and achieving sustai...