Top Plastic Recycling Machines for Efficient Waste Management
Recycle and reuse mechanical products, protect the environment and save resources.
Learn about the recycling process, methods, equipment and more.
A single-shaft shredder is an essential piece of equipment designed to efficiently handle the shredding of extruder head waste. This machine is built with a robust structure that includes a motor, a reducer with rigid gears, a rotary shaft, imported rotary knives, fixed knives, a sturdy frame, a working platform, a hydraulic ram, and an independent electrical control cabinet.
Comprehensive Plastic Recycling Equipment List with Detailed Specifications
This detailed list outlines the essential machinery and equipment used in a high-efficiency plastic recycling production line. The list includes specifications for belt conveyors, granulators, screw conveyors, separators, washing tanks, thermal dryers, de-watering machines, and more. With a total installed power of 310KW and a production capacity of 1,000 to 1,500 KG/h, this equipment setup is designed for optimal performance in plastic recycling processes. Perfect for businesses aiming to enhance their recycling operations.
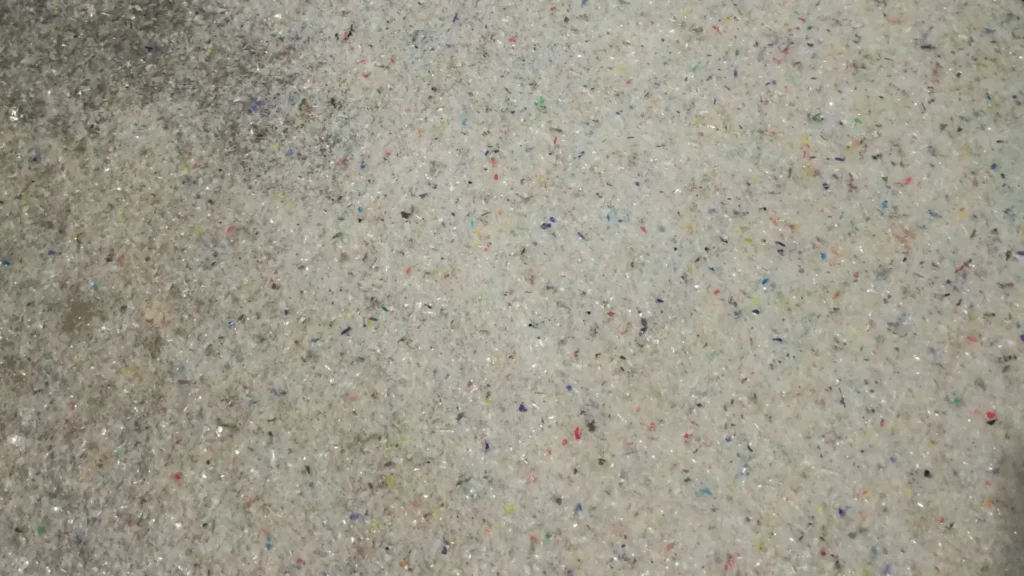
Machine Description | Specifications | Qty (piece) |
1. Belt Conveyor 1 (model#PS-800) | 1) belt width: 800㎜2) belt material: PVC3) motor power: 2.2KW4) reduction ratio: 1: 305) drive roll diameter: φ273㎜6) belt linear velocity: 0.63m/s7) driven roller diameter: φ323㎜ | 1 |
2. Granulator (model#SWHB1200) | 1) main motor: 45KW2) cutter head rotary diameter: φ630㎜3) cutter head width: 1150㎜4) No.of rotating knife: 10 pcs5) No.of stating knife: 4 pcs6) cutter material: SKD117) cutter head rotating speed: 462rpm8) cutter head material: 45 steel9) screen mesh: φ95㎜10) hydraulic open feeding hopper/ hydraulic screen changer11) hydraulic station power: 2.2KW12) capacity: 1000-1200kg/h13) transmission power: 3KW14) gear reducer model: NMRV130-3015) screw conveyor rotating speed: 20-72.5rpm adjustable16) screw vane diameter: φ250㎜17) screw space: 200㎜18) screw material: stainless steel | 1 |
3. Screw Conveyor 1 (model#LX-390) | 1) motor power: 3.7KW2) screw conveyor rotating speed: 20-72.5 rpm3) screw vane diameter: φ390㎜4) screw stroke: 300㎜5) screw material: stainless steel6) frame material: carbon steel | 1 |
4. Film and Flake Separator (model#PMFL) | 1) material: stainless steel2) frame material: carbon steel | 1 |
5. Wind-Sending System (model#FS) | 1) blower motor: 5.5KW2) pipe diameter: φ159㎜3) pipe material: stainless steel | 1 |
6. Storage For Labels (model#GLC-1) | 1) storage material: stainless steel2) volume: 2m3 | 1 |
7. Screw Conveyor 2 (model#LX-390) | 1) motor power: 3.7KW2) screw conveyor rotating speed: 20-72.5 rpm3) screw vane diameter: φ390㎜4) screw stroke: 300㎜5) screw material: stainless steel6) frame material: carbon steel | 1 |
8. Washing Tank (model#QXC1500) | 1) Width inside: 1500㎜2) Total length: 5000㎜3) Material: stainless steel4) Frame material: carbon steel5) Bottom screw motor: 5.5KW6) Discharge material screw motor: 3.7KW7) Lifting dirt screw motor power: 3KW8) Main motor power: 3KW | 2 |
9. Hot (Boiler) Washer (model#ZFL800) | 1) motor power: 7.5KW2) reducer model: BLD5-71-7.53) agitating shaft rotating speed: 20rpm4) heating power: 60KW5) boiler material: stainless steel6) transmission power: 3.7KW7) reducer model: NMRV110-208) screw rotating speed: 20-72.5rpm, adjustable9) screw vane diameter: φ290㎜10) screw spacer: 200㎜11) screw material: stainless steel | 2 |
10. High Speed Friction Washer (model#HXJ800) | 1) rotor rotary diameter: φ524㎜2) rotor material: carbon steel3) rotor rotating speed: 960rpm4) No. of rotor vane: 24 pcs5) washer body: stainless steel6) effective washing length: 2800㎜7) motor power: 37KW8) conveying angle: 15°9) driving way: belt drive | 1 |
11. Screw Conveyor 3 (model#LX-390) | 1) motor power: 3.7KW2) screw conveyor rotating speed: 20-72.5 rpm3) screw vane diameter: φ390㎜4) screw stroke: 300㎜5) screw material: stainless steel6) frame material: carbon steel | 1 |
12. De-watering Machine (model#HTS800) | 1) main motor power: 75KW2) machine inside material: stainless steel3) rotor rotary diameter: φ850㎜4) rotor material: carbon steel | 1 |
13. Thermal Dryer (model#RSI800) | 1) pipe diameter: φ159㎜2) blower power: 5.5KW3) pipe material: stainless steel4) blower model: 9-19 NO.4X55) heating power: 30KW | 2 |
14. Cyclone Separator (model#FL1200) | 1) separator diameter: φ1000㎜2) material: stainless steel | 1 |
15. Finished Product Silo (model#LC-2) | 1) silo material: stainless steel2) silo volume: 2.5m3 | 1 |
16. Electric Panel | 1 | |
Totals | Installed Power: 310KWCapacity: 1,000 – 1,500 KG/h |
Ordering
Rumtoo Recycling offers standard PET bottle washing lines for the needs of most PET recycling plants. We also offer custom design and implementation of entire PET recycling facilities based on your application, capacity, and or specifications. Either way, we’ll strive to offer the highest level of customer service and flawless communication to ensure the efficient processing of your order and projects.
Recycling post-consumer plastics like PE film, PP woven bags, and agricultural films can be a challenge due to high moisture content. Washed films typically contain up to 40% moisture, which is problematic for recyclers, leading to issues like inconsistent feeding and reduced output in recycling extruders. Traditional drying methods often fail to effectively remove this moisture, leaving up to 30% water content in the materials.
In the world of plastic recycling, separating different types of plastics efficiently and effectively is crucial. The PP PE plastic floating separation tank is one of the most essential tools in this process. This tank uses water as a medium to segregate polypropylene (PP) and polyethylene (PE) from mixed plastic streams, utilizing their distinct densities. Not only does it ensure accurate separation, but it also cleans the materials, preparing them for further processing. Let's delve deeper into how this ingenious system works and why it's a cornerstone of modern plastic recycling.
Air separators play a crucial role in plastic recycling, particularly in removing lightweight contaminants like paper and cardboard from HDPE (High-Density Polyethylene) and PET (Polyethylene Terephthalate) bottles. These machines are an integral part of recycling lines, ensuring that the recycled plastic is free from impurities, thus improving the quality of the final product.
When it comes to plastic recycling, separating contaminants from valuable materials is critical for ensuring a high-quality end product. This is where trommel machines come into play. These slow-rotating, cylindrical separation machines are essential in plastic recycling plants and larger Material Recovery Facilities (MRFs) dealing with municipal waste. Despite their leisurely pace, trommels are incredibly effective at filtering out smaller contaminants from recycling streams, making them a key component in the recycling process.
Our Disk Separator is a highly efficient machine designed to separate material streams based on size. Whether you're dealing with plastics, paper, metals, or other mixed materials, this machine ensures precise separation tailored to your needs. Its customizable features and robust construction make it a top choice for various industrial applications.
In the world of plastic recycling, efficiency is key. As recycling plants handle large volumes of compacted HDPE and PET bottles, the need for an effective solution to break apart these bales becomes paramount. Enter the vertical debaler machine—a powerful, automated solution designed to streamline the recycling process, reduce manual labor, and enhance overall productivity. This article explores the mechanics, benefits, and technical specifications of this innovative machine, making it an indispensable asset for any plastic recycling facility.
When it comes to maximizing the efficiency of recycling operations, particularly in removing non-ferrous metals from materials like post-consumer PET bottles, the advanced eddy current separator (ECS) stands out as a crucial piece of machinery. This sophisticated separator is not only vital in the plastic recycling industry but also plays an integral role in a variety of other sectors, ranging from glass and timber processing to the recycling of electronic scrap and automobile shredder residue.
Our eddy current separators are crucial pieces of machinery for separating aluminum and other non-ferrous metals from various process streams. Since non-ferrous metals typically hold higher value, recovering this stream is a vital aspect of numerous recycling facilities across the globe.
Our wet plastic bottle label remover is an innovative recycling machine capable of removing more than 95% of the labels from intact plastic bottles. As this machine utilizes water to detach the labels, the bottles are cleaned simultaneously, making this an excellent option to enhance your current or new PET bottle recycling operation.
Plastic recycling is a dynamic industry that requires precision, efficiency, and the right equipment to ensure optimal results. One crucial tool that enhances the recycling process is the suspension magnetic separator. These machines are designed to recover valuable ferrous metals and remove harmful tramp ferrous metals, thereby protecting downstream equipment and improving the quality of recycled products.