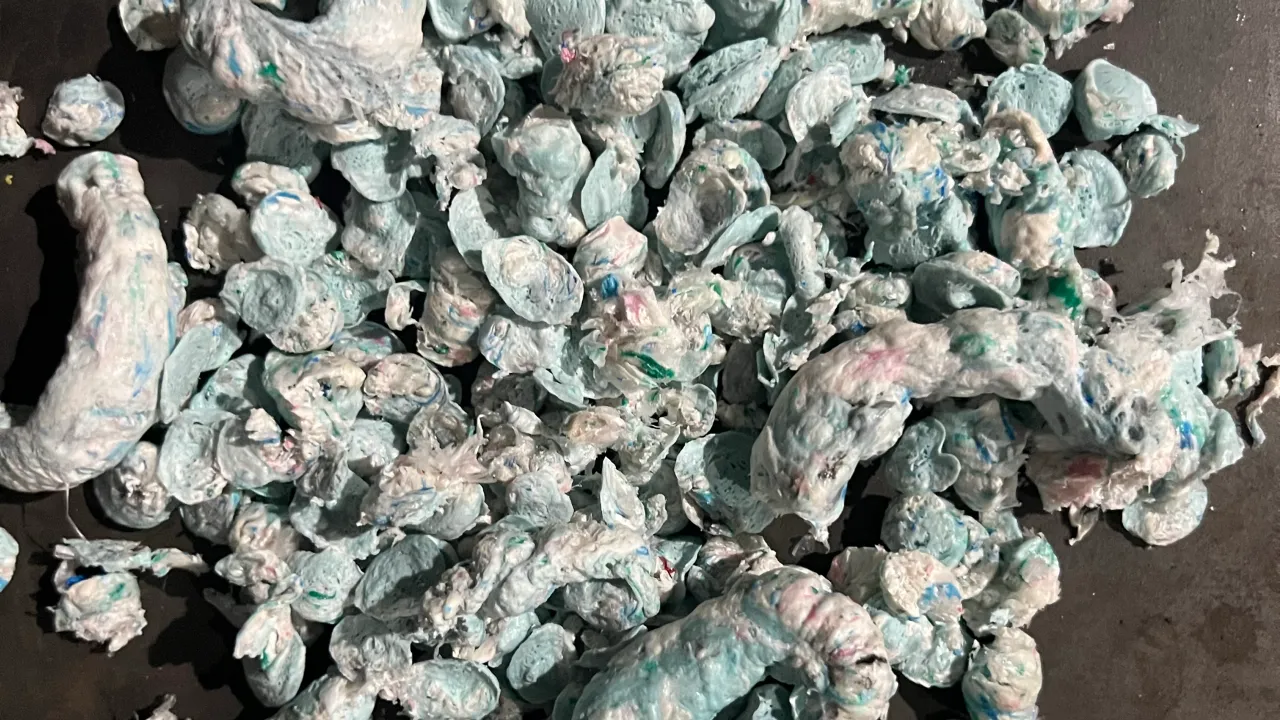
Densified Material
Material after film densification
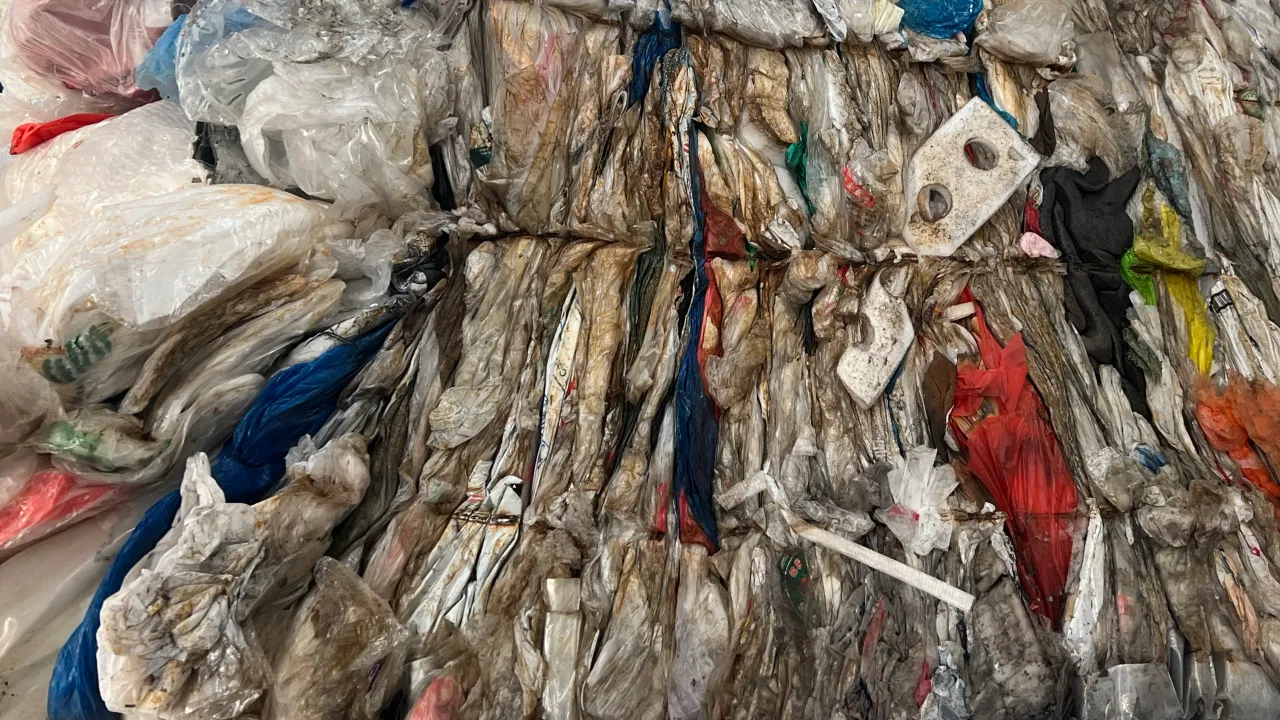
Waste Plastic Film
Plastic film waste generated in daily life and industrial production
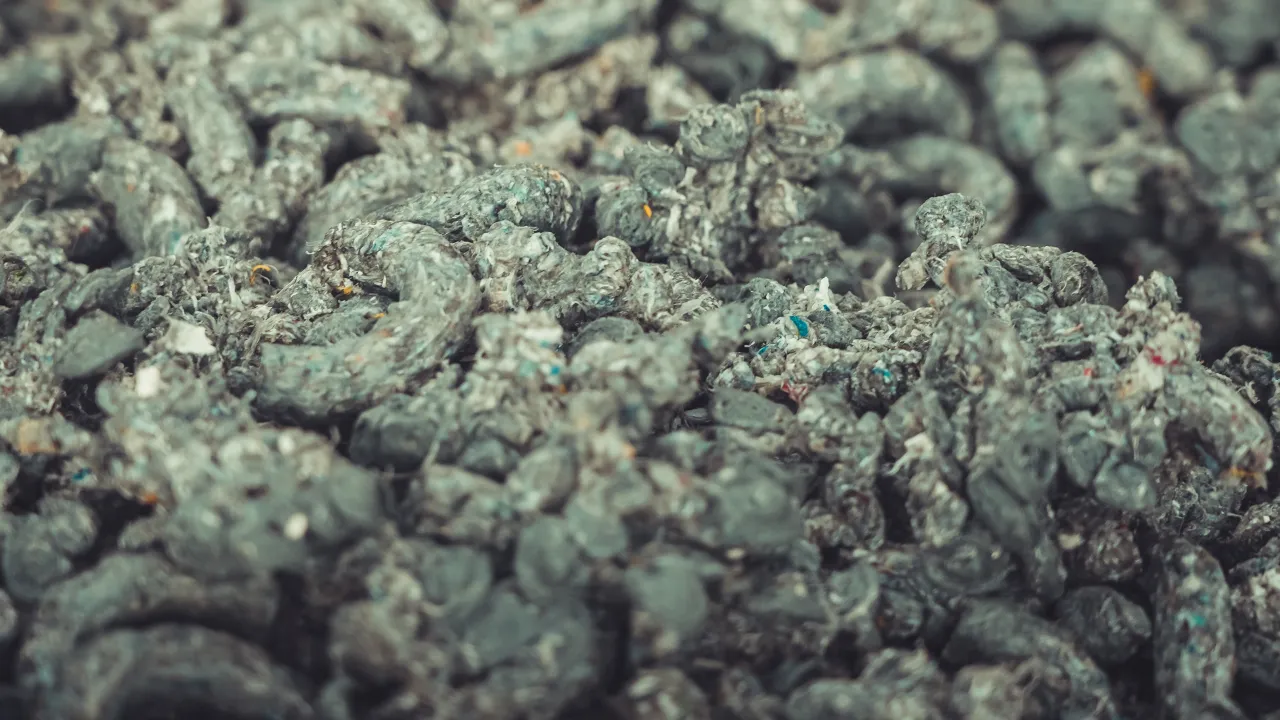
Densifying Material
For plastic film/bags after washing
Challenges in Plastic Film Recycling
Recycling post-consumer plastic films presents significant challenges due to their high moisture content:
- High Moisture Content:
Washed film typically contains up to
40% moisture, posing difficulties for recyclers. - Ineffective Drying:
Standard vertical dryers struggle to remove moisture from lightweight film flakes, often leaving
20-30% residual water after drying. - Recycling Issues:
Excessive moisture leads to:- Inconsistent feeding in the recycling extruder
- Reduced output efficiency
These challenges highlight the need for innovative drying solutions in the plastic film recycling process.
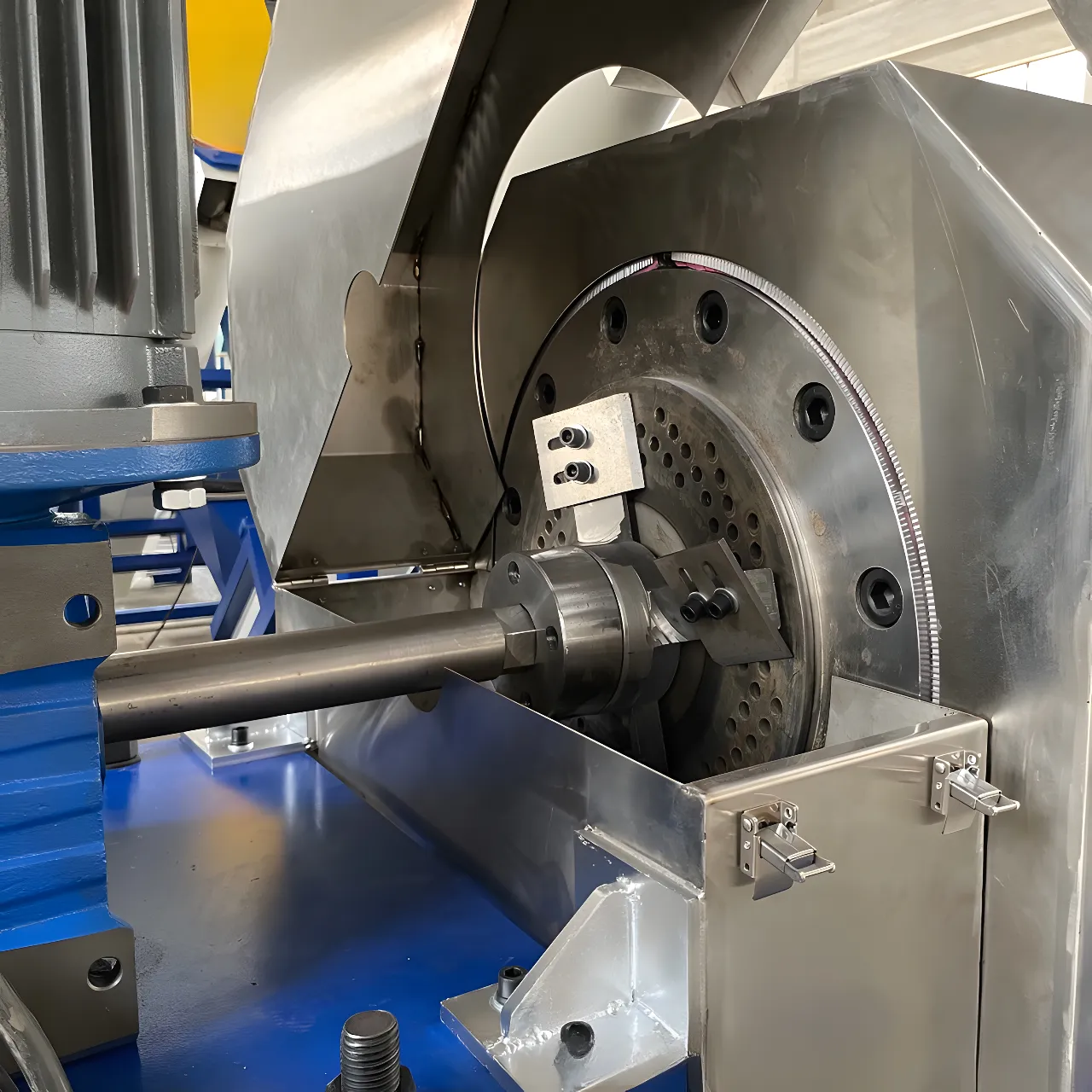
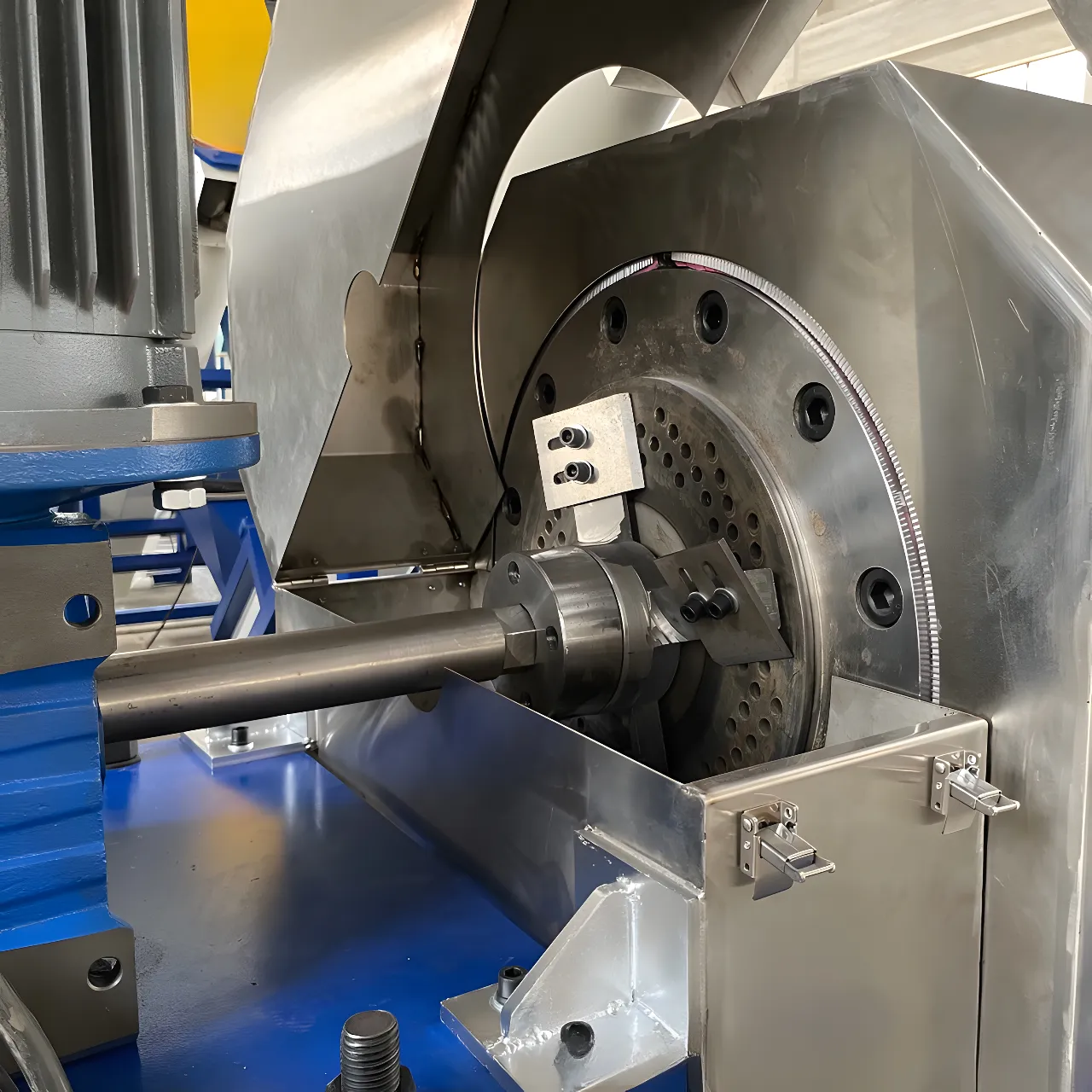
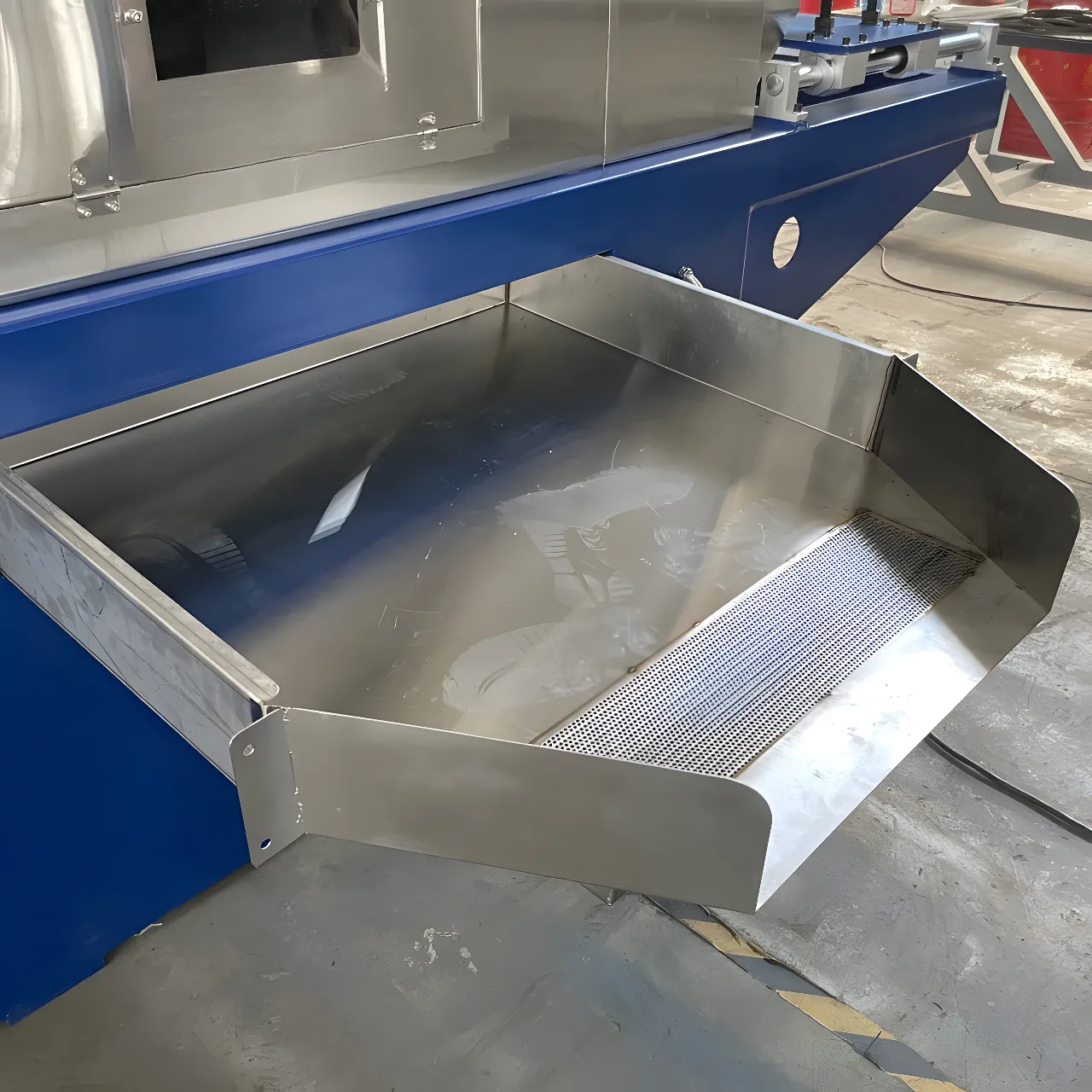

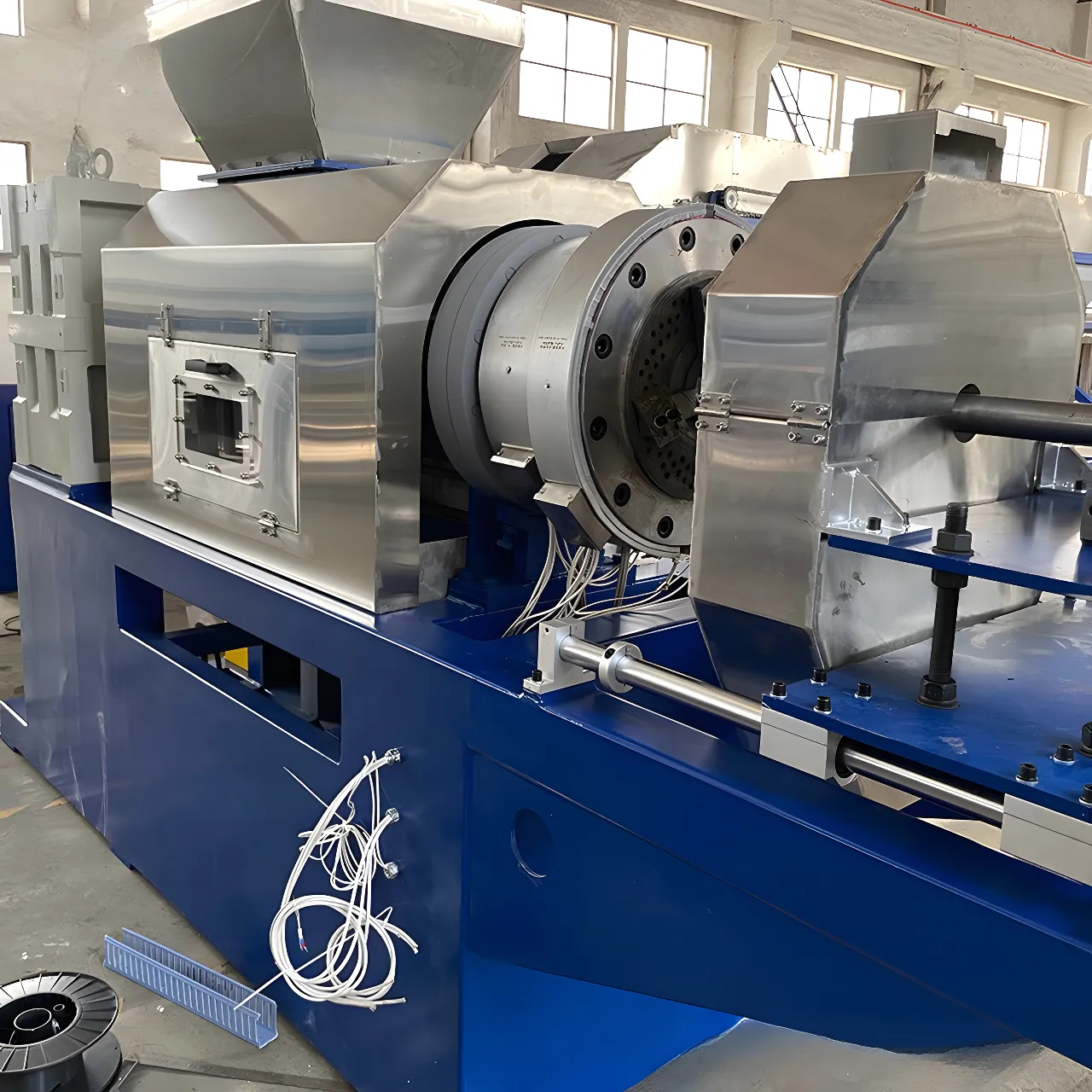
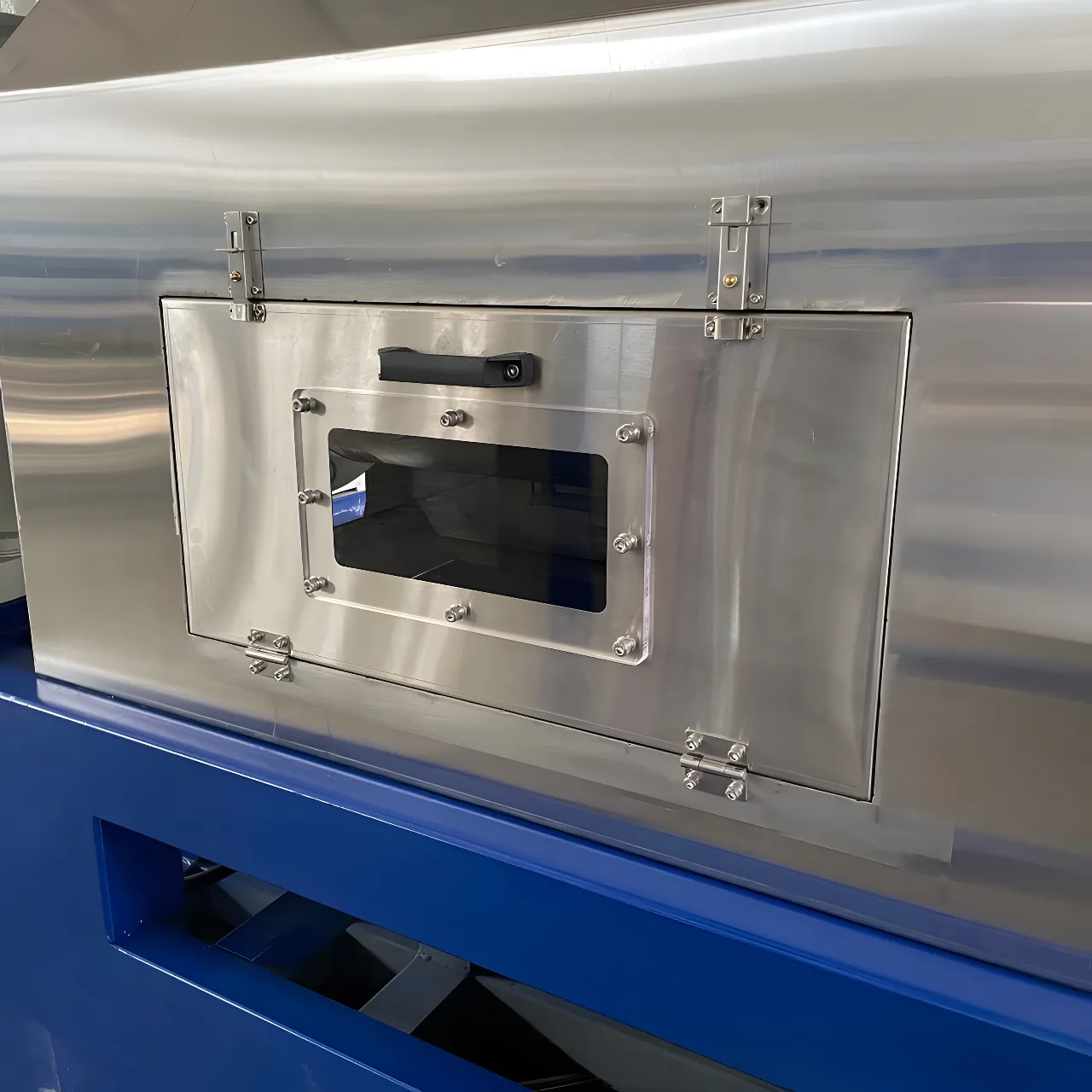

Working Principle
1. Feeding
Washed plastic films, typically still containing moisture, are fed into the machine through a conveyor or feeding system.
2. Squeezing Process
- Inside the machine, the plastic films are subjected to a high-pressure squeezing process.
- A rotating screw within the machine forces the material through a specially designed perforated barrel or mesh.
- The intense pressure created by the screw and the narrow spaces within the barrel forces the water out of the plastic films.
3. Dehydration
- The moisture is squeezed out through the perforations, leaving the plastic films much drier.
- The expelled water is then collected and drained away.
4. Extrusion
- After the squeezing process, the dried plastic material is extruded in the form of pellets or loose flakes.
- A cutting mechanism may be used to chop the extruded material into smaller pieces, making it easier for further processing.
5. Discharge
The dried and compressed plastic material is discharged from the machine, ready for further processing, such as pelletizing or direct reuse.
Main Features
1. Efficient Moisture Reduction
After washing, the system reduces water moisture levels in film flakes from a typical range of 10-35% down to a remarkably low 1-5%.
2. Density & Volume Optimization
The process transforms loose film flakes into solid, high-density lumps. This reduces volume, leading to faster, easier, and more stable feeding into the extruder.
3. Accelerated Drying
Drying times are significantly faster for both washed film and woven waste compared to traditional methods like centrifugal drying or hot air blow drying.
4. Minimized Heat & Material Degradation
The drying process generates less heat, minimizing material degradation and ensuring higher value and reusability of the recycled pellets.
5. Extrusion-Ready Material
The system effectively prepares the material for the subsequent extrusion-pelletizing process, maximizing efficiency and output.
Benefits of This Technology
1. Improved Recycling Efficiency
Faster drying, better feeding, and reduced material degradation contribute to a more efficient recycling process.
2. Higher-Quality Recycled Pellets
Reduced moisture and minimized degradation lead to higher-quality recycled pellets with greater reusability.
3. Environmental Benefits
Improved recycling efficiency and less material degradation contribute to a more sustainable approach to plastic waste management.
Technical specifications
Model | Screw Diameter (mm) | Heating Power (kw) | Applicable Material | Main Motor Power | Screw Material | Heating Method | Output (kg/h) |
---|---|---|---|---|---|---|---|
RTM250 | 250 | / | PP/PE | / | High Nitrogen Steel | Electromagnetic Heating | 200-350 |
RTM300 | 300 | / | PP/PE | / | High Nitrogen Steel | Electromagnetic Heating | 400-550 |
RTM320 | 320 | / | PP/PE | / | High Nitrogen Steel | Electromagnetic Heating | 600-750 |
RTM350 | 350 | / | PP/PE | / | High Nitrogen Steel | Electromagnetic Heating | 800-1000 |
Advantages
1. Enhance Extruder Efficiency
Boosts output capacity and effectiveness of the pelletizing extruder and the overall recycling process.
2. Enhance Pellet Quality
After squeezing, the volume of the material decreases, making feeding into the pelletizing extruder easier and more consistent. Consequently, the quality of the final product (recycled pellets) also enhances.
Integration with Recycling Washing Line
1. Maximize Output
Optimizes output when operating in conjunction with the compactor-extruder-pelletizing type of recycling machine.
2. Specially Designed
Engineered to fit between the washing line and plastic recycling extruder to elevate output and efficiency.
3. Workflow
Washing line → plastic squeezer dryer → plastic recycling extruder
Warranty & Installation
Each recycling machine includes a 1-year limited warranty. We provide installation services, with our engineers visiting your site to assist with the setup process. Arrangements for regular maintenance crews and operational consultants can also be made.
Inquire Now
To get the latest prices and lead times, send us a message using the form below.
I am text block. Click edit button to change this text. Lorem ipsum dolor sit amet, consectetur adipiscing elit. Ut elit tellus, luctus nec ullamcorper mattis, pulvinar dapibus leo.