Plastic crusher/granulator are essential machines in the plastic recycling process, transforming discarded plastic into reusable “regrinds” or “flakes.” This article provides a comprehensive overview of plastic granulators, covering their working principles, types, factors affecting granulation speed, wet granulation, proper usage, and maintenance.
How Plastic Crusher/Granulator Work
Plastic crusher/granulator utilize a simple yet effective mechanism. Cutting knives mounted on a high-speed rotor spin within a cutting chamber containing stationary knives. As plastic scrap enters the chamber, the rotating and stationary knives work together to shred the plastic into smaller pieces. A screen at the bottom of the chamber allows the sufficiently small regrinds to pass through, while larger pieces continue to be cut until they are small enough.
Types of Plastic Crusher/Granulator
While the basic concept remains the same, different granulator designs cater to specific needs. Three main types exist:
- Double Scissor Cut (or Double Angle Cut): This design features parallel rotor and stationary knives angled slightly. This configuration ensures a consistent cutting gap, resulting in lower temperature increases, minimal power consumption, and cleaner cuts.
- Chevron or V-type Rotor: Knives are arranged in a V-shape, pushing plastic towards the center even as they dull. This design is particularly effective for handling thicker plastic components.
- Helical Rotor: Knives are arranged in a helix within a closed rotor, making this type robust and suitable for processing thick, cross-sectional plastic parts.

Factors Affecting Crusher/Granulator Speed
- Several factors influence the speed at which a granulator can process plastic:
- Type of Material: Softer plastics like polyethylene (PE) and polypropylene (PP) are easier to cut than tougher engineering plastics like ABS, Nylon, and PC.
- Size of Cutting Chamber & Knives: Larger chambers and longer knives allow for processing larger volumes of plastic at once.
- Quality of Knives: High-quality knives made from durable materials like D2 / SKD 11 steel are essential for efficient and consistent cutting.
- Quantity of Knives: More knives generally lead to faster cutting, but the optimal number depends on the granulator design.
- Electric Motor: A more powerful motor spins the rotor faster, increasing cutting action.
- Screen Size: Smaller screen holes result in finer regrinds but require longer processing times.
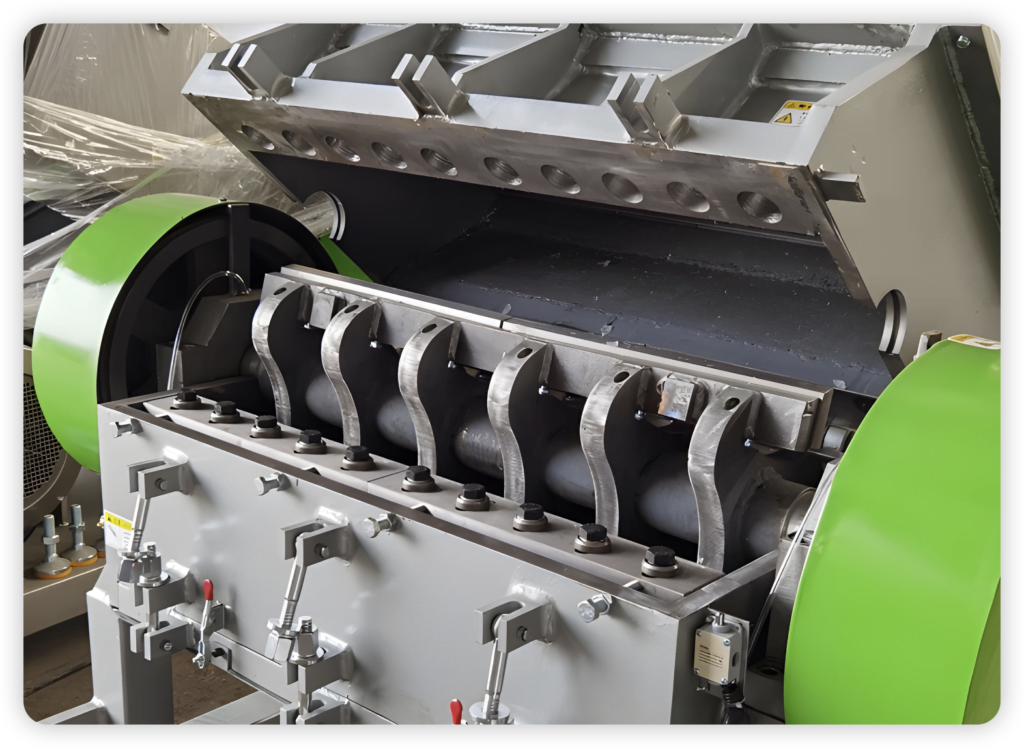
Wet Crusher/Granulator
Wet Crusher/granulator incorporate water jets or hoses within the cutting chamber. This offers several advantages:
- Partial Cleaning: Water helps wash away contaminants during size reduction.
- Lubrication: Water acts as a lubricant between knives, reducing friction and heat buildup.
- Reduced Knife Wear: Lower friction and temperature significantly extend knife lifespan.
Wet crusher/granulator are commonly used in plastic film washing lines.
Proper Crusher/Granulator Usage
- To ensure safe and efficient operation, follow these guidelines:
- Never start the granulator with material inside the cutting chamber.
- Keep foreign objects away from the granulator during operation.
- Avoid feeding large lumps or purgings.
- Empty the collection bin regularly to prevent overloading.
- Do not batch feed; shredders are better suited for this.
- Turn the granulator on before feeding plastic.
- Avoid overloading the granulator.
- Regularly inspect and maintain knives.
- Rotate the granulator screen to extend its life.
- Purge the granulator before turning it off.
- If using a blower, stop the granulator before stopping the blower.
Maintenance
- Regular maintenance is crucial for prolonging the lifespan of your granulator and preventing costly repairs.
- Sharpen and Rotate Knives: Regularly sharpen and rotate both rotor and stationary knives to ensure efficient cutting and reduce wear and tear.
- Remove Foreign Objects: Keep the cutting chamber free of foreign objects like metals that can damage knives and the rotor.
- Monitor Screen: Ensure the screen is not clogged, as this can lead to rotor jamming and motor burnout.
- Lubricate Motor and Bearings: Regularly lubricate the motor and bearings to ensure smooth operation.
- By understanding the principles, types, and proper usage of plastic granulators, you can effectively utilize this essential tool in your plastic recycling process.