Plastic is ubiquitous, and its durability is indisputable. However, its environmental impact is often profound. A practical solution to mitigate plastic waste lies in recycling, spearheaded by devices such as plastic granulators. But how exactly do these machines transform discarded plastic into reusable material? Let’s explore!
The Transformation from Plastic Waste to Granules
The process starts with the collection and sorting of plastic waste. Since different plastics necessitate distinct processing techniques, precise sorting is essential. Once categorized, the plastic progresses through several stages within the granulator:
- Shredding: Large pieces of plastic are reduced to smaller, manageable fragments. Imagine a colossal blender converting milk jugs into tiny pieces.
- Washing: The fragments undergo a thorough cleansing to eliminate dirt, labels, and other contaminants that might compromise the granule quality.
- Drying: Any residual moisture is extracted to avert clumping in the subsequent steps.
- Extrusion: The dried fragments are melted and extruded through a die, shaping the molten plastic into elongated, spaghetti-like strands.
- Cooling: These strands are quickly cooled, stabilizing their form.
- Cutting: The solidified strands are then chopped into small pellets, termed as plastic granules.
These granules are primed for reuse in manufacturing new plastic products, thereby closing the recycling loop.
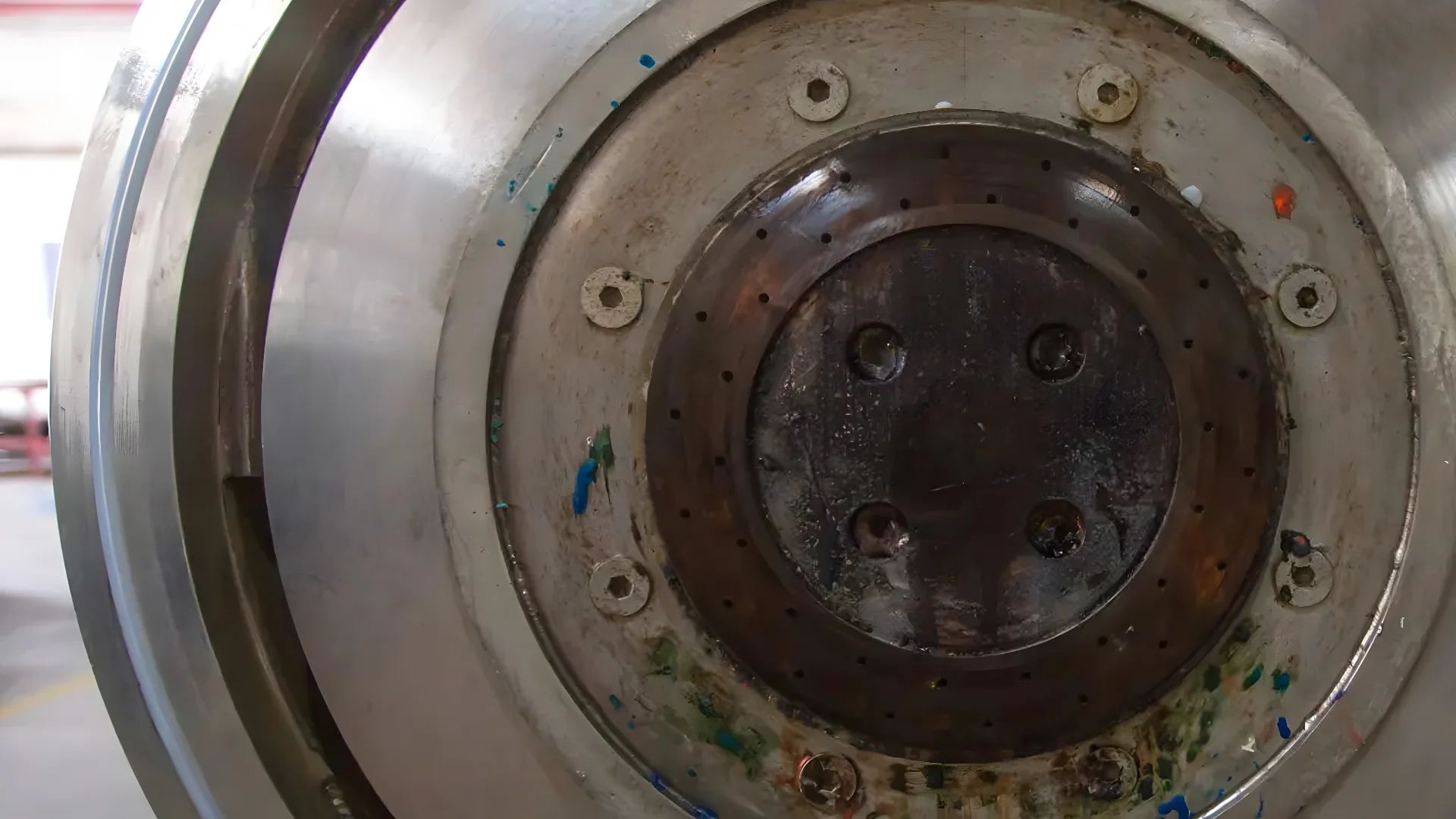
The Benefits of Plastic Granulators
Plastic granulators are pivotal in reducing plastic waste, offering several advantages:
- Environmental Preservation: Recycling plastic curtails the production of new plastic, conserving resources and diminishing landfill accumulation.
- Cost Efficiency: Employing recycled granules is generally more economical than new plastic, providing financial benefits for manufacturers.
- Diverse Usability: The granules are versatile, suitable for manufacturing a broad array of products, including packaging, bottles, furniture, and construction materials.
Understanding the operations of plastic granulators illuminates their crucial contribution to a sustainable future. These machines are a robust solution to the global challenge of plastic waste, converting discarded materials into valuable assets.
FAQs About Plastic Granulators
- What plastics can be processed?
- A variety of plastics such as PET, HDPE, LDPE, PP, and PVC are suitable for granulation, each requiring tailored processing settings.
- What is the size of the granules?
- The granules typically measure between 2 to 10 millimeters in diameter, though sizes can vary based on the granulator and application needs.
- Are the granules safe?
- Yes, the granulation process includes stringent contaminant removal, ensuring the granules are safe for diverse uses.
- Is granulation energy-intensive?
- Granulation consumes less energy compared to producing new plastic, making recycling a more sustainable practice.
- How to learn more about local plastic recycling?
- Local government bodies and environmental groups often provide details on recycling initiatives. Contact your municipal waste management authority or search online for nearby recycling options.