Our PP / PE plastic film water-ring pelletizing system integrates the functions of crushing, compacting, plasticization, and pelletizing all in a single step. At the heart of this system is our highly efficient single screw extruder with advanced heat stabilization technologies resulting in superior quality pellets that help to enhance your bottom line.
In addition to pelletizing plastic films, this system can also be utilized for raffias, filaments, bags, woven bags, and re-pelletizing of densified materials. The final products produced by this pelletizing system are in the form of pellets or granules that can be directly used in production lines for film blowing, pipe extrusion, and plastics injection, etc.
Working Principle
- Feeding: As a standard design, plastic scraps such as film and raffias are conveyed into the compacting room through a belt conveyor; to handle rolls’ scraps, a roll hauling-off device is an optional feeding method. The feeding speed of the conveyor belt or roll hauling-off is fully automatic based on how full the compactor’s room is. A metal detector can be integrated with the belt conveyor and can interlock with the control system to alert and halt the system in case metal is detected in the feeding section.
- Shredding and compacting: The rotary blades of the compactor will cut up incoming scraps. Frictional heating caused by high-speed rotary blades will heat and shrink the scraps just below their agglomerating point. Optimally designed guide structures compact the material and direct it into the extruder screw. It crushes, dries, and compacts the material, which enables a rapid and stable feeding from the compactor directly into the extruder.
- Plasticization and degassing: A specialized single screw extruder is applied to gently melt the pre-compacted material. The plastic scraps will be thoroughly melted and plasticized in the first stage extruder, and the plastic will be extruded by the second stage extruder. With a double-zone vacuum degassing system, volatiles such as low molecular compounds and moisture will be removed efficiently, making it especially suitable for heavily printed film and material with some water content.
- Melt filtration: Segmented filtering principle is used, with preliminary filtering in the first extruder and fine filtering in the second extruder, to reduce the frequency of changing filtering sieves. The requirements for the filter technology depend on the quality of the input material as well as the planned use of granules.
- Water-ring Pelletizing: Die-face water-ring pelletizing system is set as the standard granulating method. Advanced dewatering vibration sieve combined with horizontal-type centrifugal dewatering presents high-performance dried pellets.
Technical Specifications
Model Size | Efficiency Volume (Liter) | Motor Power (KW) | Diameter of screw (mm) | L/D | Motor Power (KW) | Throughput Rate (kg/h) |
---|---|---|---|---|---|---|
SJ80 | 300 | 37 | 80 | 36 | 45/55 | 160-220 |
SJ100 | 500 | 55 | 100 | 36 | 90/110 | 300-380 |
SJ120 | 800 | 90 | 120 | 36 | 132 | 450-480 |
SJ140 | 1000 | 110 | 140 | 36 | 160/185 | 500-650 |
SJ160 | 1200 | 132 | 160 | 34 | 220/250 | 800-1000 |
SJ180 | 1400 | 315 | 180 | 34 | 315 | 1000-1200 |
Additional Images
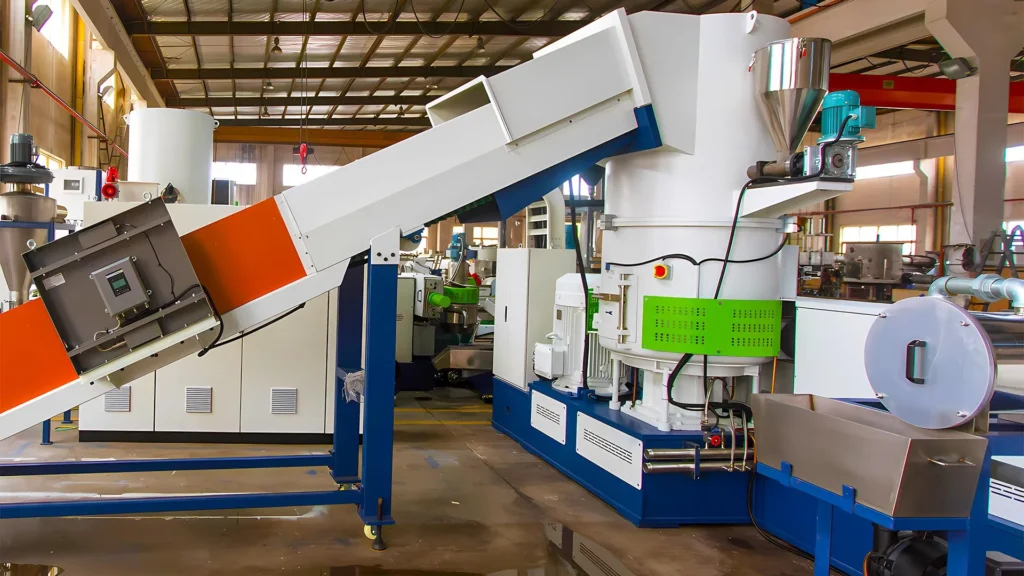
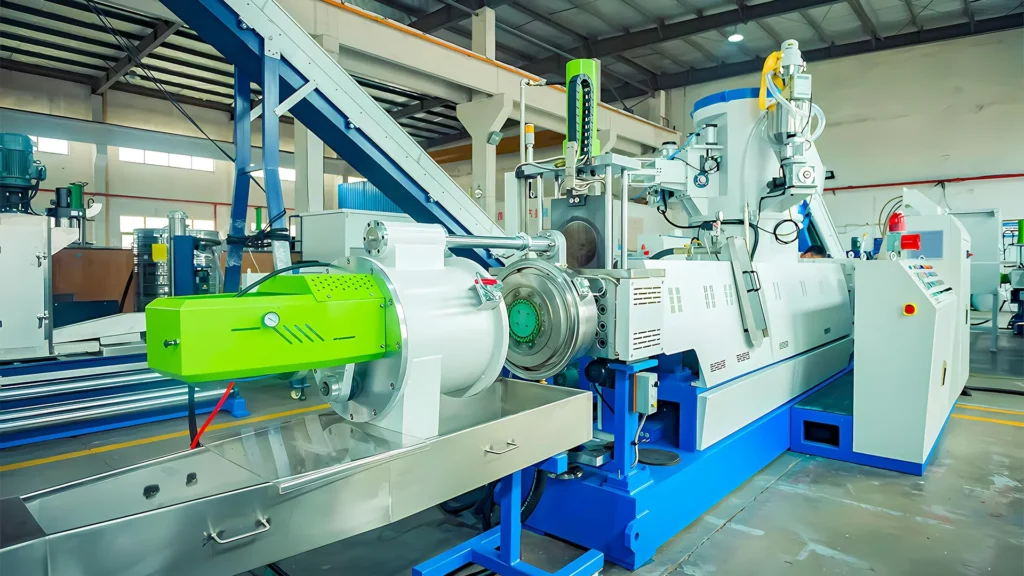
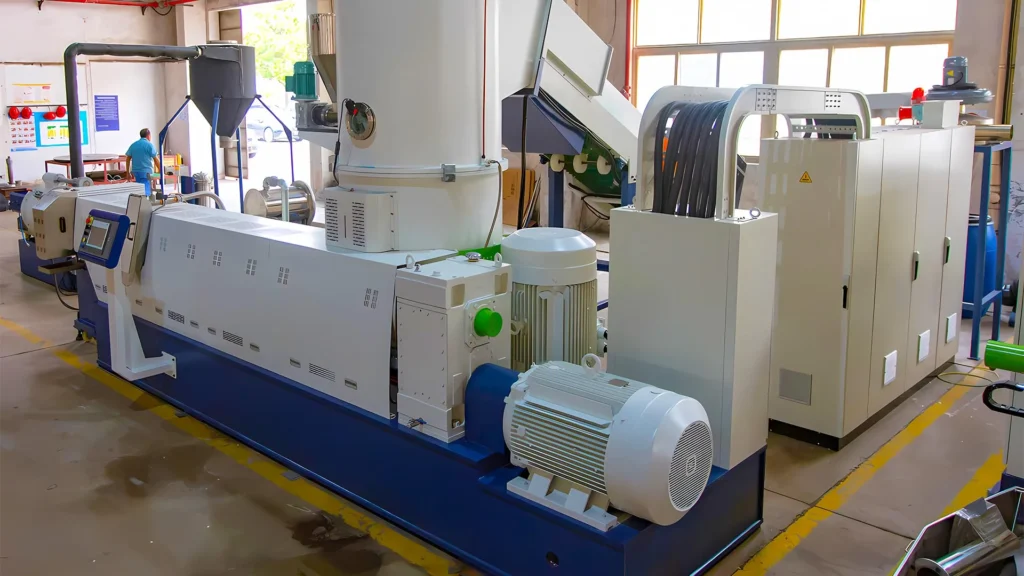
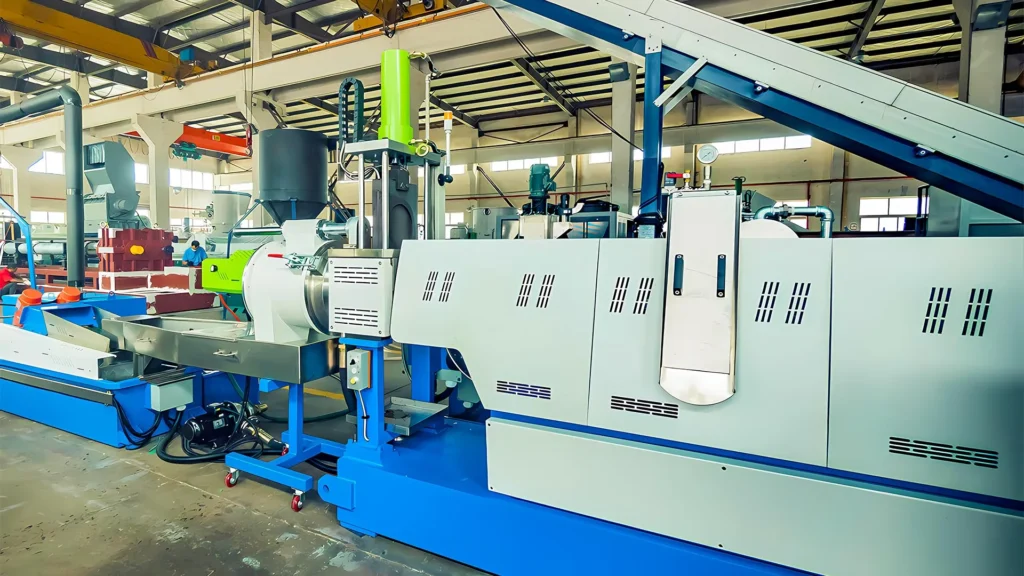
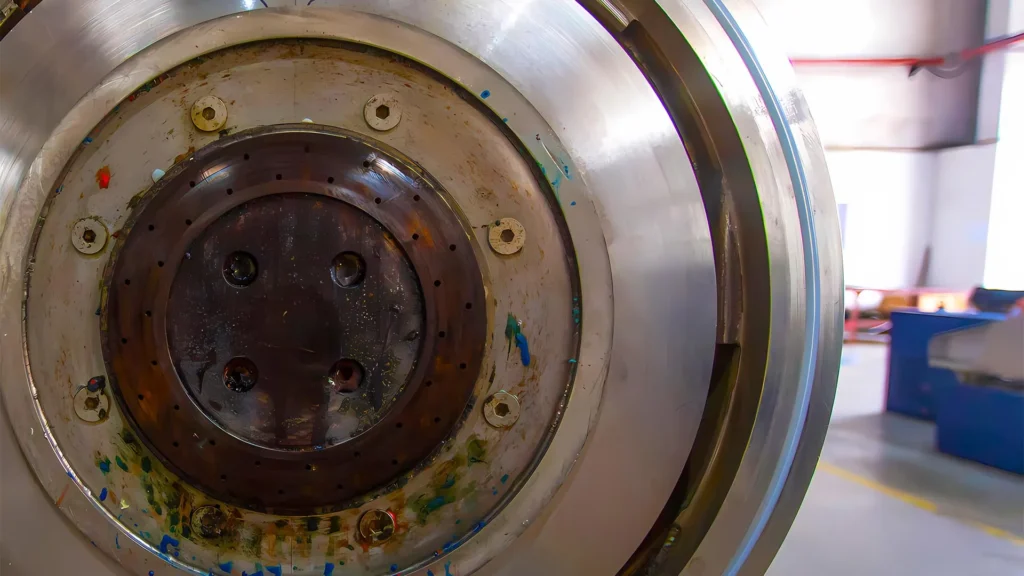
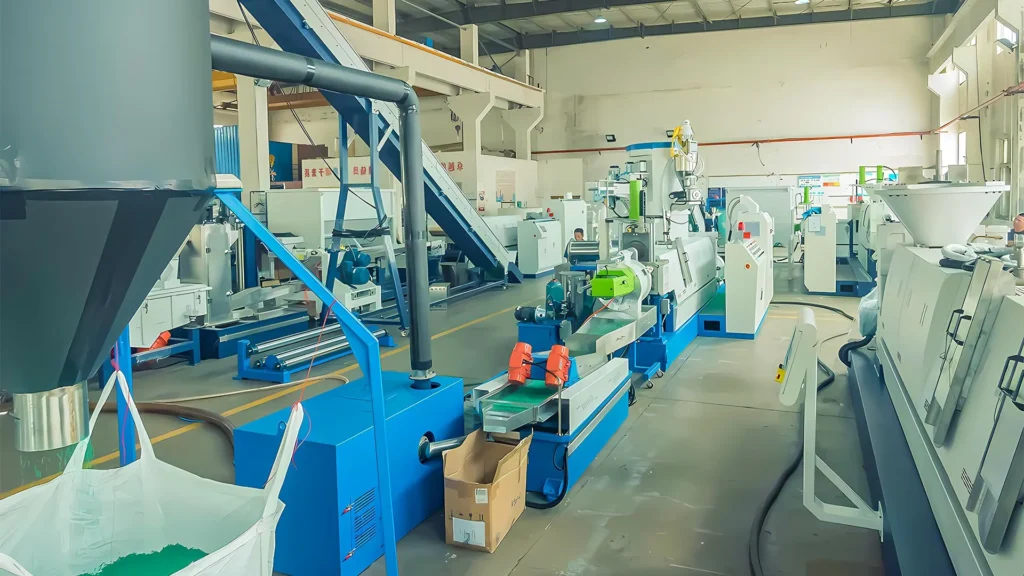
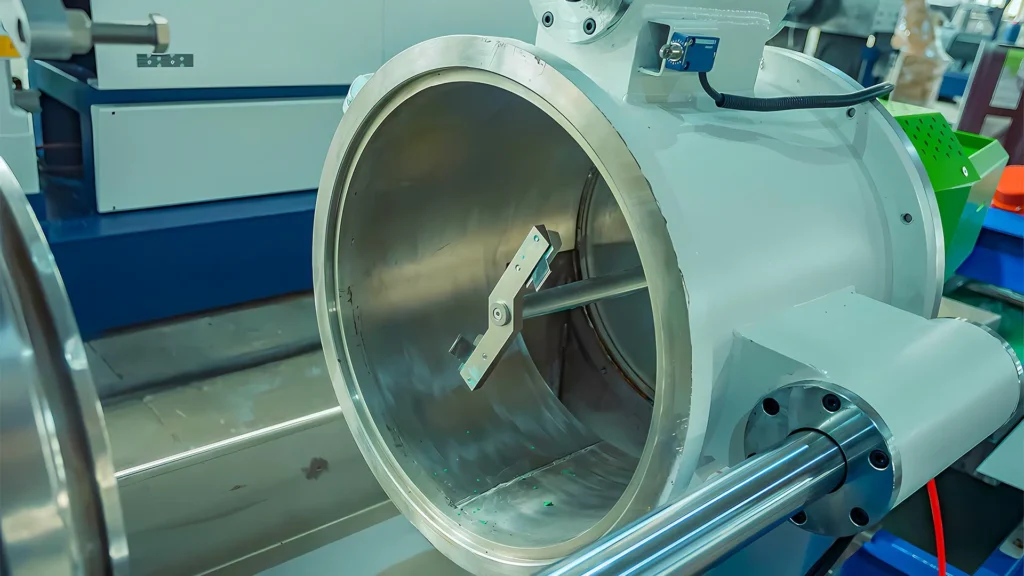
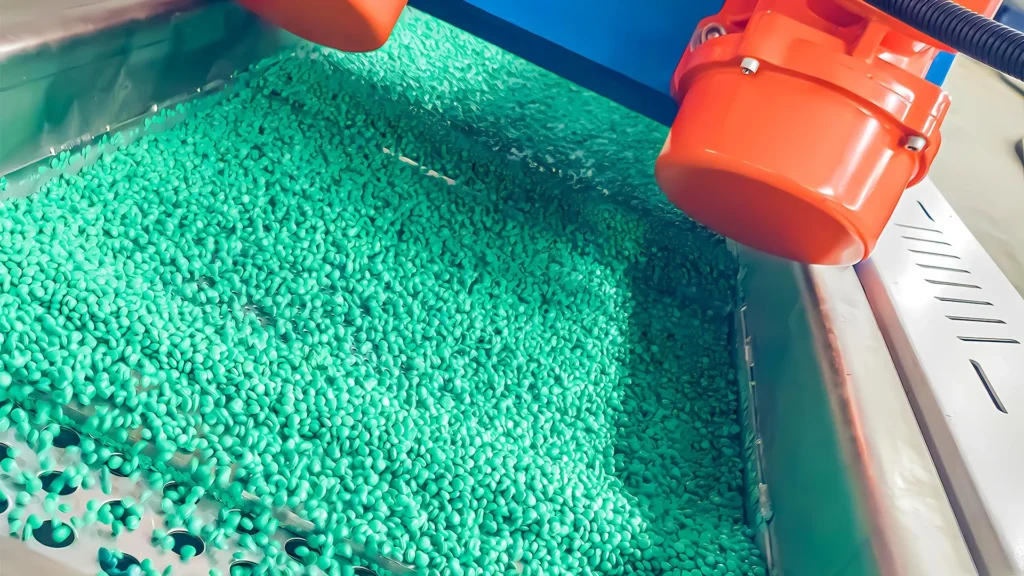