Unwrapping the Future of Recycling: The Plastic Film Squeezer’s Role in the Circular Economy
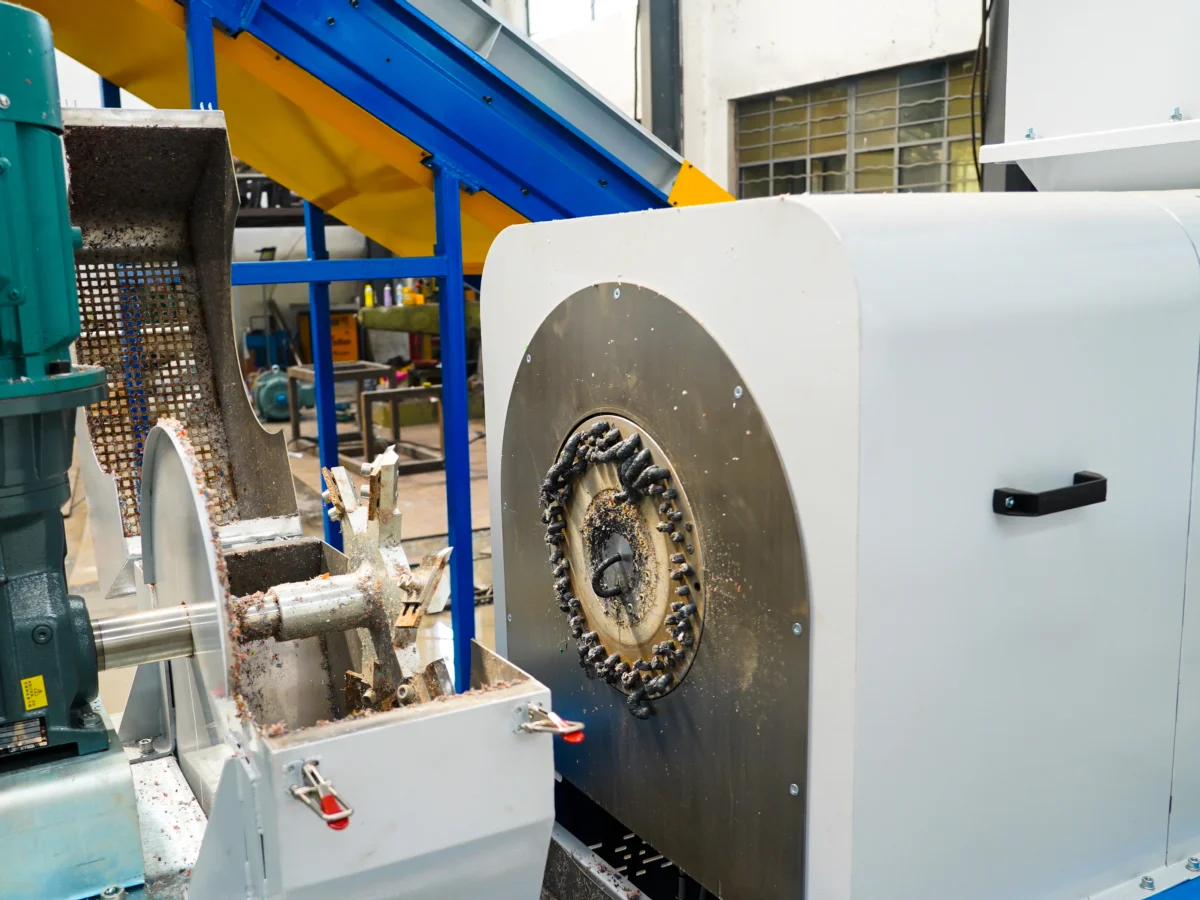
The escalating crisis of plastic waste demands innovative solutions that not only recycle but also contribute to a circular economy. The “Plastic Film Squeezer” stands out as a beacon of progress in this domain, offeri...