Premium Shredding Technology
Explore the core composition and operational principles of our single-shaft shredders, vital equipment designed for efficient waste management. Our machines are engineered to optimise the shredding process through precision engineering and durable construction.
Applications: Plastic purging, runners, pallets, wood, branches, and bones.
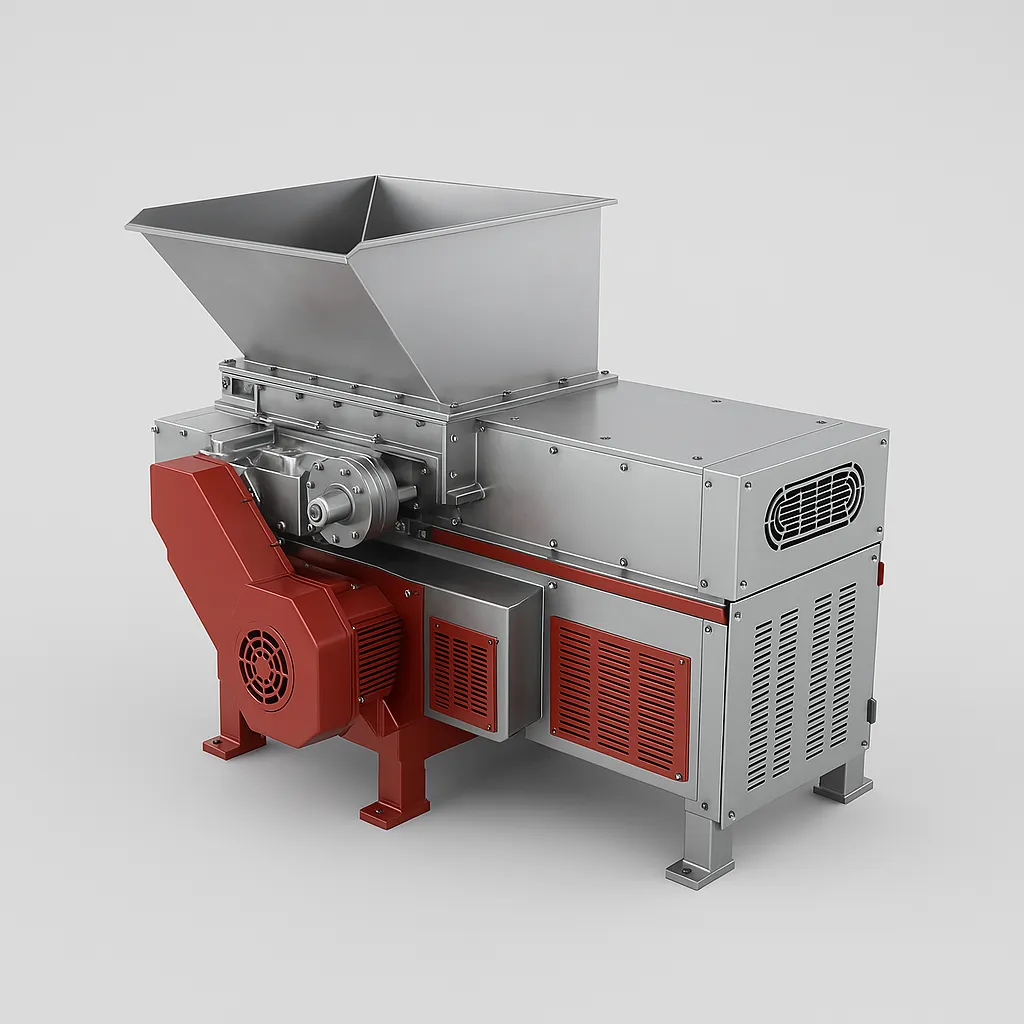
Components of a Single-Shaft Shredder
Our single-shaft shredders are primarily used to break down various waste materials. Here's a detailed look at the main components:
Shaft
Central to the shredder, the shaft drives the blades to effectively crush materials. Typically crafted from robust high-strength steel, it's engineered to endure heavy-duty operation.
Blades
Mounted on the shaft, these crucial elements shear, tear, and grind the input materials. Made from durable alloy steel, the blades ensure optimal shredding with extended longevity.
Feed Hopper
This component guides waste into the shredder. Its design varies based on the type of materials processed and the specific requirements of the operation.
Discharge Outlet
Situated at the base, it facilitates the exit of shredded particles, designed to accommodate different shredded material sizes.
Drive System
This includes a motor, reducer, and coupling to transfer power efficiently from the motor to the shredder's mechanical parts.
Operational Principle
Materials enter through the feed hopper, get fragmented by the blades, and are propelled until they reach the desired size, exiting through the discharge outlet. This process involves multiple mechanical forces like friction and shearing, ensuring efficient waste breakdown.
Key Benefits:
- High-quality, consistent output
- Minimal maintenance requirements
- Adjustable screen size for precise control
- Energy-efficient operation
- Robust construction for industrial environments
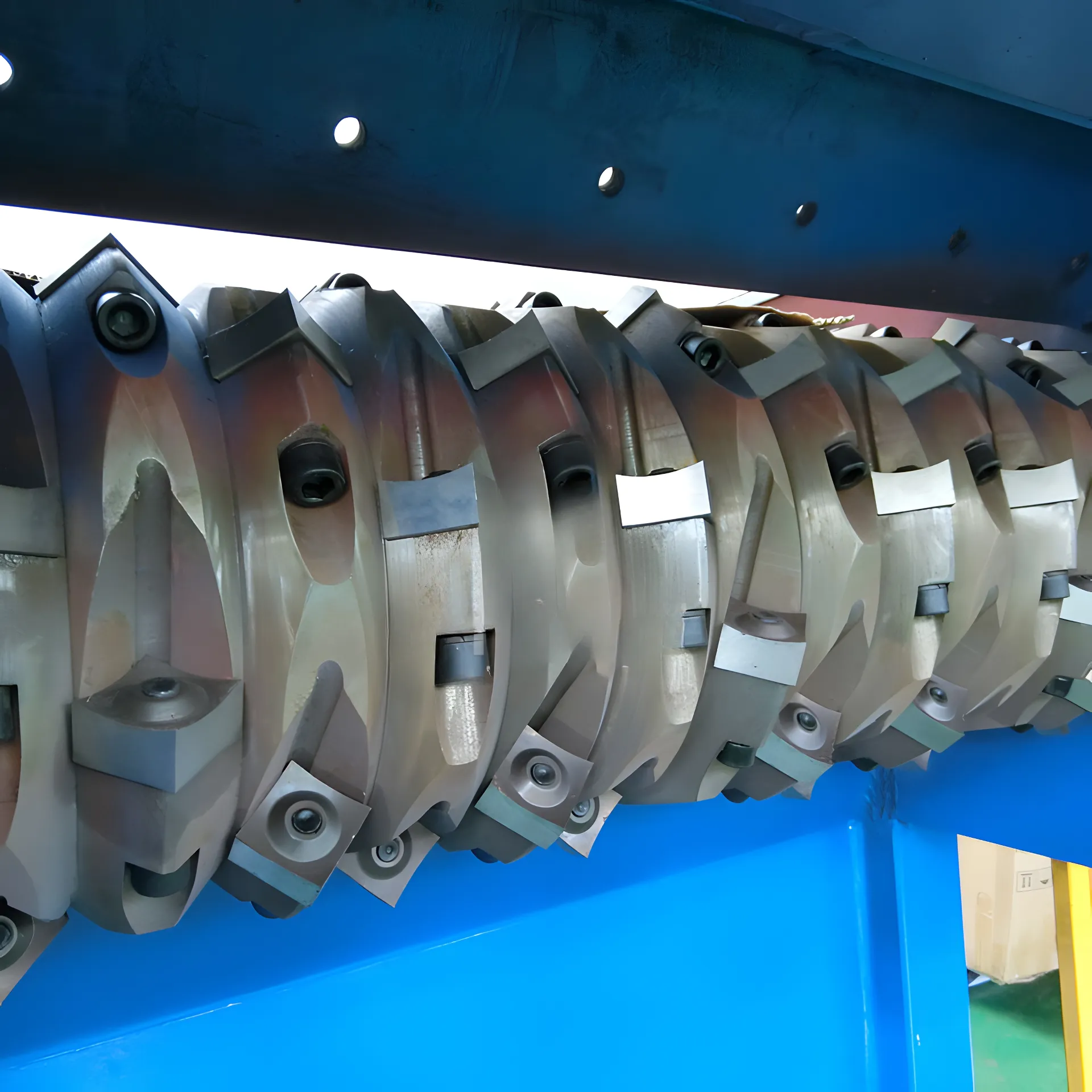
Single-Shaft vs Double-Shaft Shredders
Feature | Single-Shaft Shredder | Double-Shaft Shredder |
---|---|---|
Ideal Materials | Solid, thick pieces (plastic purging, runners, pallets, wood) | Hollow, lightweight plastics (PE films, PP tubes, HDPE drums) |
Cutting Mechanism | Single rotor with fixed blades | Dual rotors with shear blades |
Maintenance | Lower maintenance requirements | Higher maintenance requirements |
Cost-Effectiveness | More cost-effective for suitable materials | Higher initial investment, higher throughput |
Output Uniformity | Good uniformity | Excellent uniformity |
See Our Shredders in Action
Watch our single-shaft shredders process various materials with precision and efficiency.
Technical Specifications
Model | RTMS-600 | RTMS-800 | RTMS-1000 | RTMS-1200 |
---|---|---|---|---|
Capacity(kg/h) | 30kW | 45kW | 2*37kW | 2*45kW |
Hydraulic motor power | 4kW | 4kW | 5.5kW | 5.5kW |
Knife material | SKD11 | SKD11 | SKD11 | SKD11 |
Main motor power | Φ400 | Φ400 | Φ450 | Φ500 |
Rotary diameter(mm) | 85 | 85 | 80 | 70 |
Rotating speed(rpm/min) | 400-600 | 600-800 | 800-1200 | 1500-2000 |
ENQUIRIES
All recycling machines come with a 1-year limited warranty.
To receive the latest prices and lead times, please send us a message using the form below.
[…] Shredder blades, as wear parts, need periodic replacement. Given their cost, manufacturers recommend purchasing a spare set of blades with the shredder equipment for an economical and practical solution. When blades need replacing, simply swap them out, recondition the worn blades with wear-resistant welding, and sharpen them with a blade grinder. This cycle of use not only saves money but also ensures the shredder operates without delay—a true win-win. […]