In the world of plastic recycling, efficiency and cleanliness are paramount. Whether you’re running a large-scale recycling operation or a smaller setup, the key to producing high-quality recycled plastic is ensuring that contaminants are effectively removed. Enter the high-speed friction washer—a machine specifically designed to elevate your recycling process by delivering cleaner, more refined plastic with less water waste. This article delves into the inner workings, benefits, and technical specifications of this essential piece of machinery.
High-Speed Friction Washer: A Must-Have for Plastic Recycling Plants
The high-speed friction washer is a powerhouse in the plastic recycling industry, playing a critical role in the cold-water washing process. Designed to make the most of friction, this machine cleans plastic materials such as flakes, films, and regrinds, ensuring that the final product is free from dirt, paper, cardboard, and other contaminants.
How It Works
At the heart of the friction washer is a long shaft rotating at impressive speeds, often exceeding 1,000 rotations per minute (RPM). This shaft is equipped with tilted panels or paddles that create a high degree of friction as the plastic pieces are forced to rub against each other. The machine’s core is encased in a circular mesh screen, which plays a pivotal role in filtering out contaminants.
Working Principle:
- Plastic Stream Entry: The plastic stream enters the washer at the lower end of the machine, which is set at a steep incline. This design ensures that the plastic remains in the washer for an extended period, enhancing the cleaning process.
- Friction and Pressure: As the plastic is spun at high speeds within the cavity, it is pushed against the mesh screen. The intense friction and pressure generated by the spinning motion loosen contaminants from the plastic.
- Water Efficiency: Unlike traditional washers that drench the entire cavity in water, the high-speed friction washer utilizes strategically placed water jets and nozzles. This method conserves water while still ensuring that the plastic is thoroughly cleaned.
- Clean Plastic Output: The cleaned plastic exits the washer at the top end, ready for further processing or recycling.
Technical Specifications
Understanding the technical specifications of the friction washer is crucial for selecting the right model for your recycling plant. Below is a table outlining the specifications of various models available:
Model | Motor Power | Main Shaft Diameter | Rotating Speed | Capacity |
---|---|---|---|---|
HXJ400 | 37KW | 400mm | 1400 RPM | 400 – 800 KG/H |
HXJ550 | 45KW | 550mm | 1200 RPM | 600 – 1000 KG/H |
HXJ750 | 55KW | 750mm | 1080 RPM | 1200 – 2000 KG/H |
Note: CE certification is available, and larger, more powerful models can be customized upon request.
Benefits of Using a High-Speed Friction Washer
- Superior Cleaning Efficiency: The high-speed friction washer excels in removing a wide range of contaminants, ensuring that the recycled plastic is of the highest quality.
- Water Conservation: By using water jets and nozzles instead of flooding the cavity, the machine reduces water usage, making the recycling process more sustainable.
- Scalable to Your Needs: With various models available, recycling plants can select a washer that meets their specific capacity requirements. Custom models can also be requested for even higher capacities.
- Durable Design: Built for longevity, the machine’s robust design minimizes downtime and maintenance costs, ensuring continuous operation in demanding environments.
Additional Images
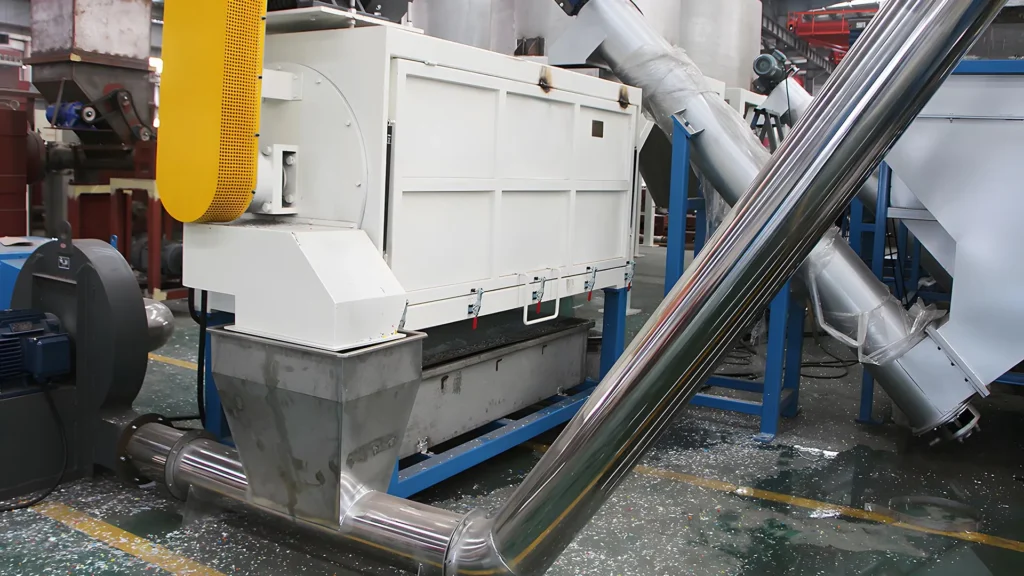
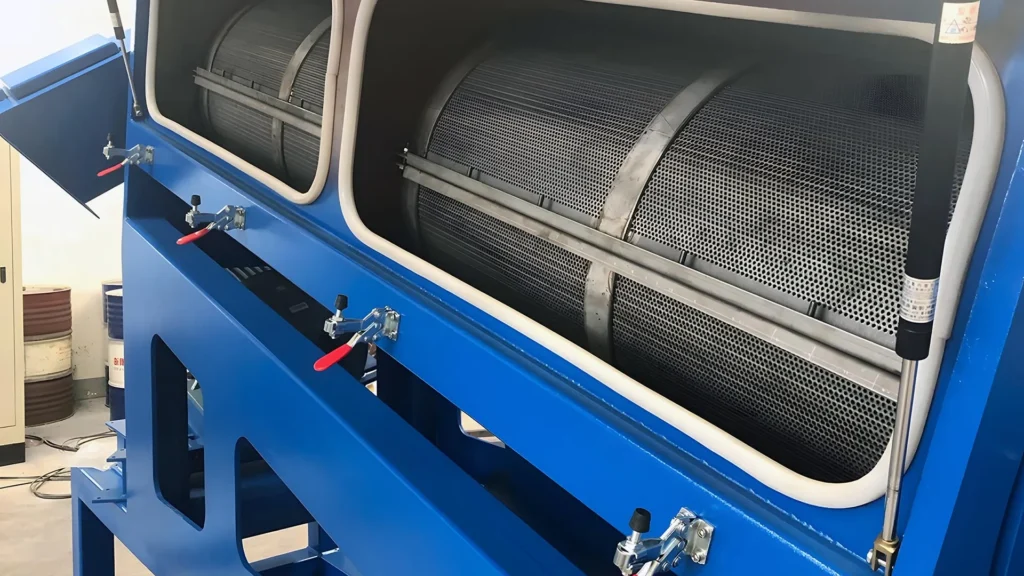
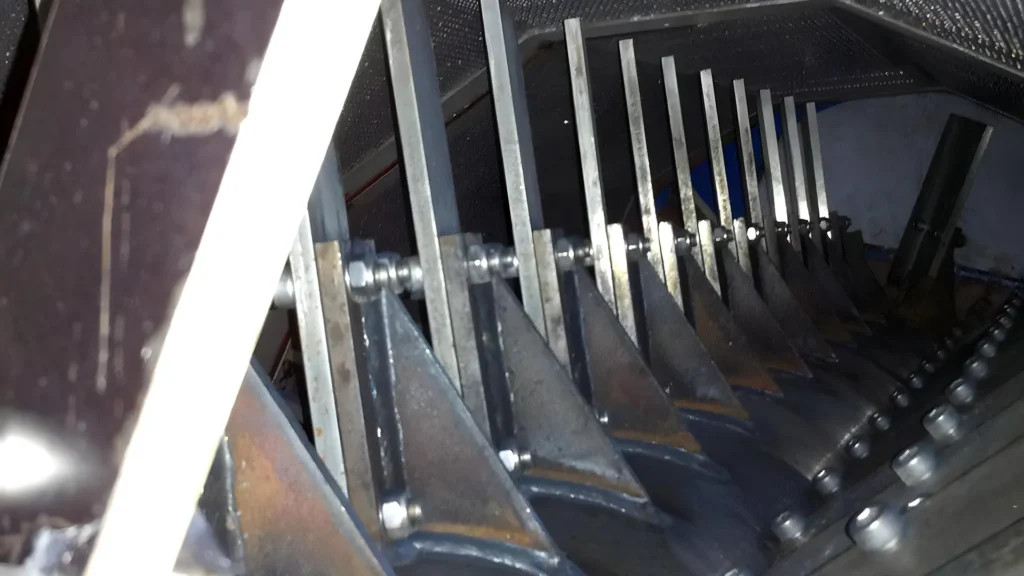
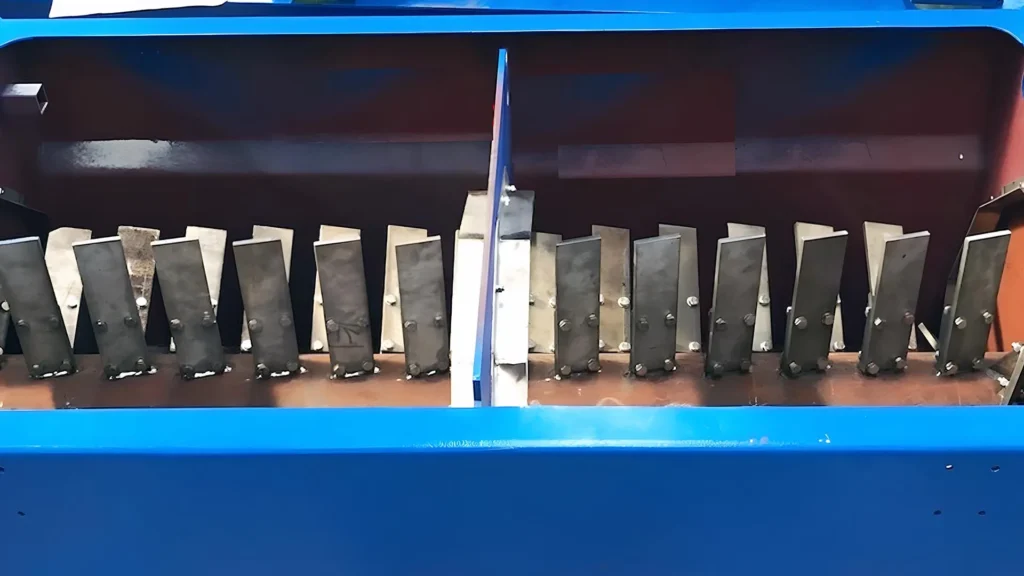

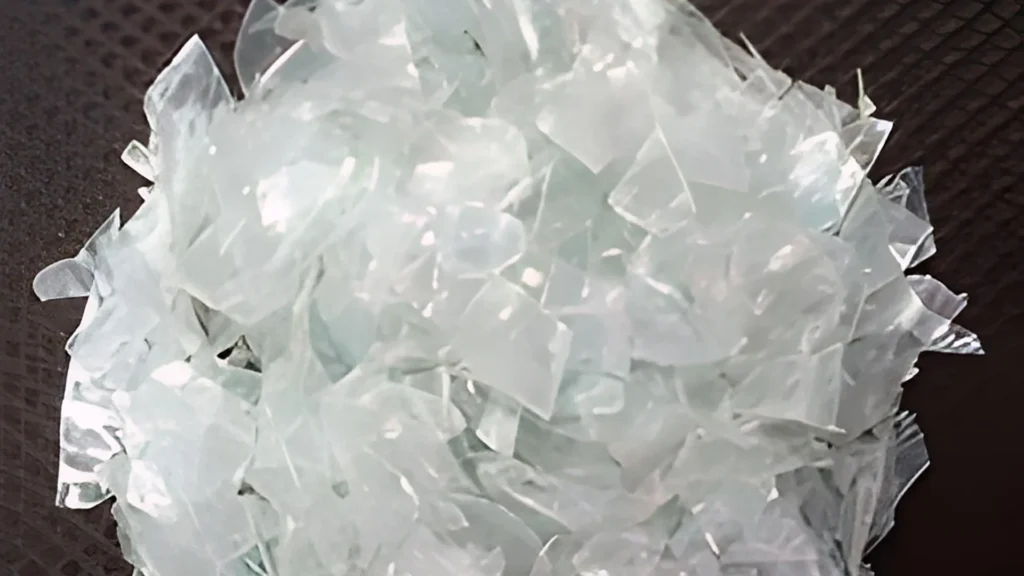
Conclusion
For any plastic recycling plant aiming to produce a clean final product stream, the high-speed friction washer is an invaluable asset. Its ability to effectively clean plastic while conserving water makes it a standout choice in the recycling industry. Whether you’re upgrading your current setup or looking to invest in a new machine, the high-speed friction washer offers the performance, efficiency, and durability you need.
Warranty & Installation
Each recycling machine includes a 1-year limited warranty. We provide installation services, with our engineers visiting your site to assist with the setup process. Arrangements for regular maintenance crews and operational consultants can also be made.
For inquiries regarding pricing, lead times, or customized models, feel free to reach out through the provided contact form.