Polypropeenipussien ja kuitukankaiden kierrättäminen: kattava opas
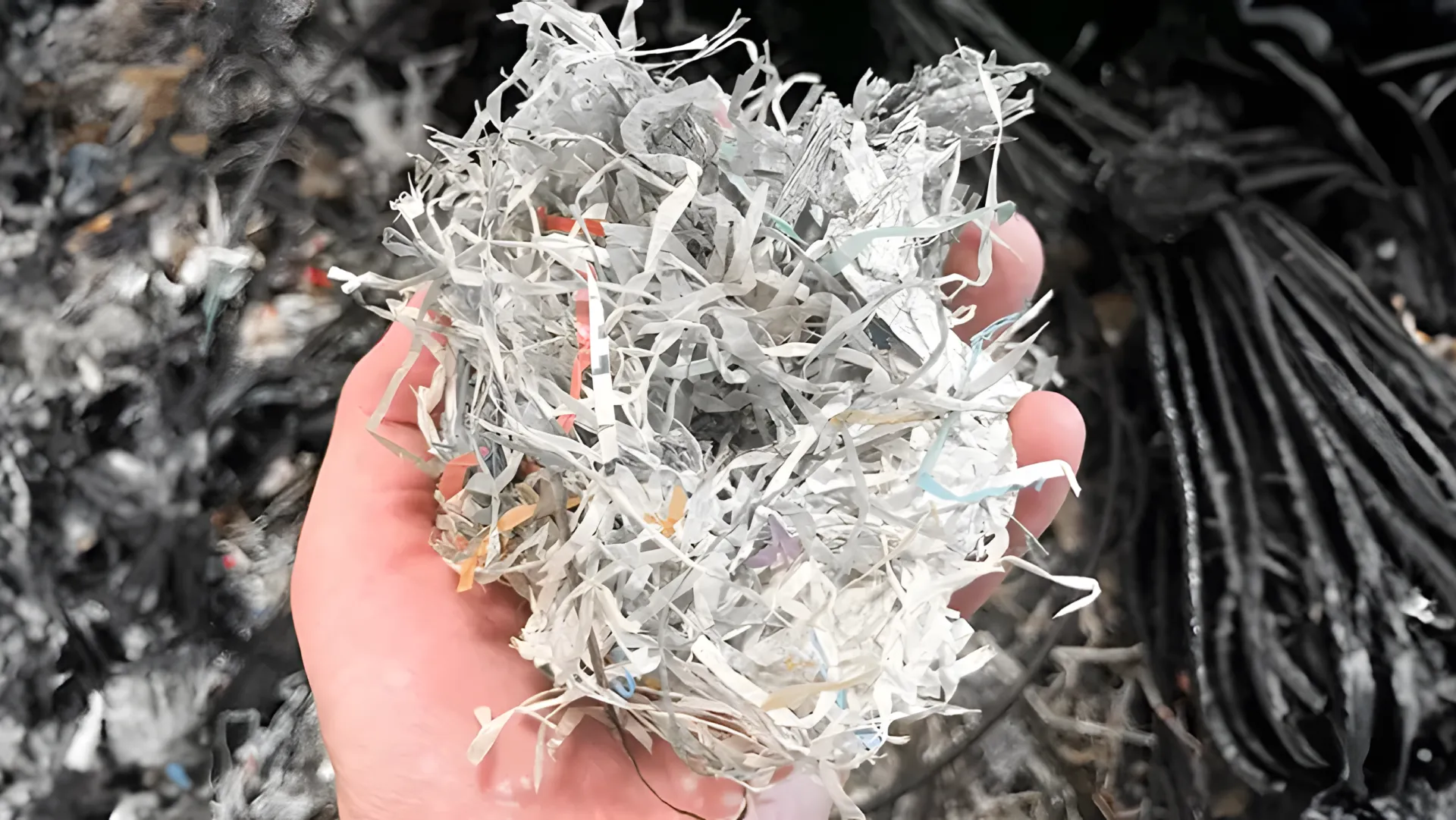
Polypropeeni (PP) pussit, joita tavataan yleisesti eri teollisuudenaloilla, tunnetaan kestävyydestään, keveydestä ja kosteudenkestävyydestään. Näillä pussilla, mukaan lukien kudotut pussit ja bulkkipussit, on merkittävä rooli...